Complex Part Produced with One Setup
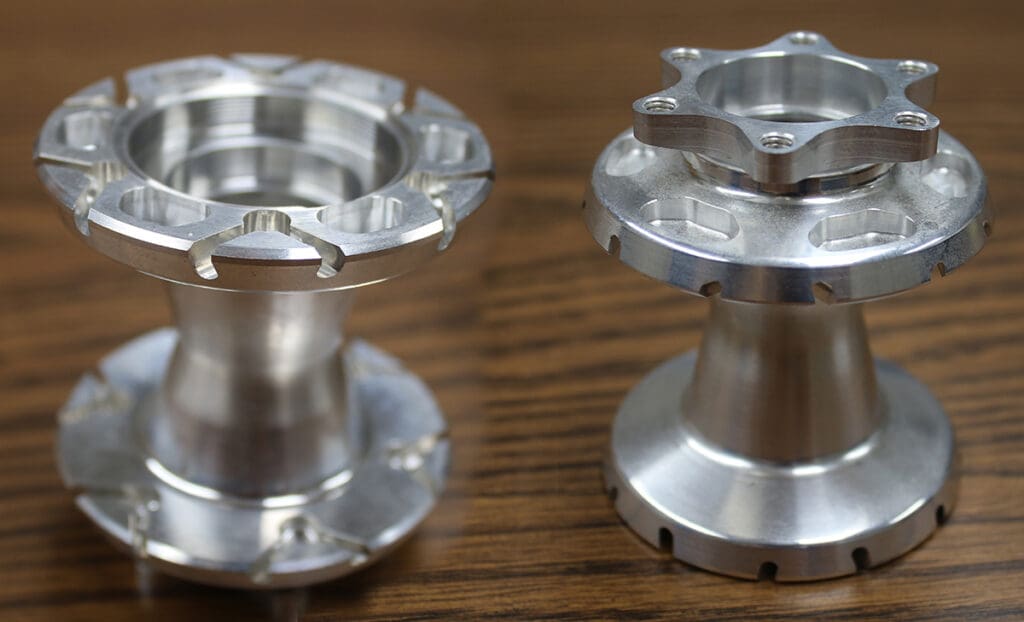
This aluminum part was produced with one setup. Note the intricate geometry, recessed bores, counterbores, threaded grooving with tapered bores. A bike manufacturer needed a wheel hub part built out of a single piece of aluminum. The workpiece was very complex. It required multiple channels and recessed bores, multifaceted surface geometry, counterbores and threaded grooving […]
Large, Multi-Axis Aluminum Part
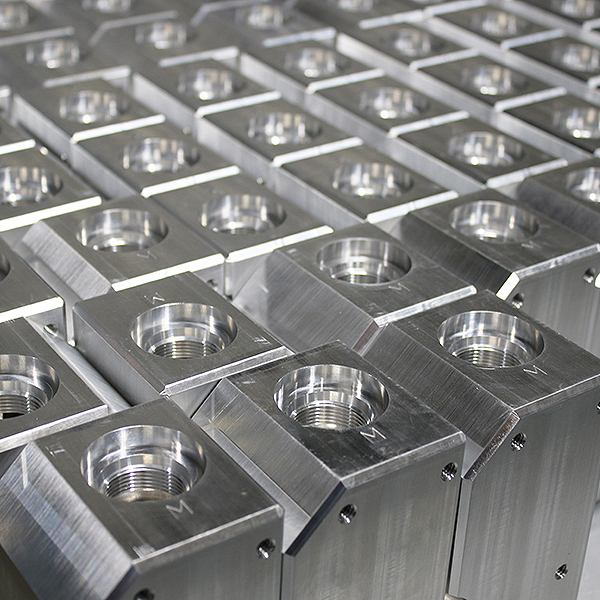
An engine manufacturer was in need of a valve body made with an aluminum alloy. The part was designed with O-ring ports for connecting fluid lines, bores for sensors and other components. They needed only a few hundred of these parts produced. This part had very tight tolerances for the size and location of features […]
Multi-Axis, Ultra-Small Titanium Parts
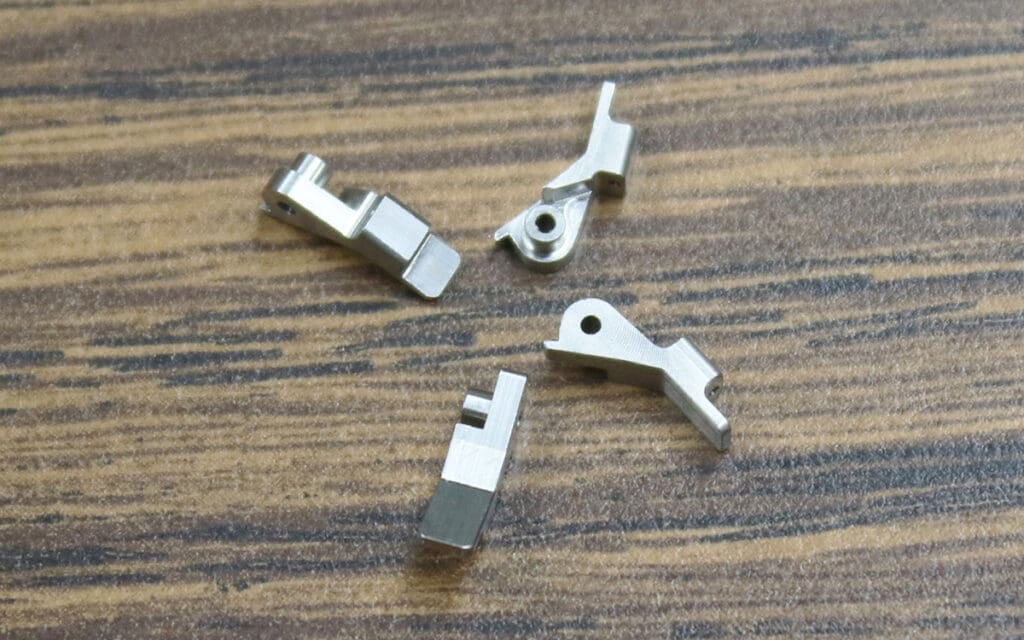
A manufacturer of military aerospace products required tiny titanium parts. The specifications required the parts to be produced with multiple angles, through holes and counterbores. The customer also needed a small quantity run on these parts. Boyer Machine specializes in small, milled parts. They have decades of experience machining complex metal alloys that other machine […]
Milled Plastic Medical Parts
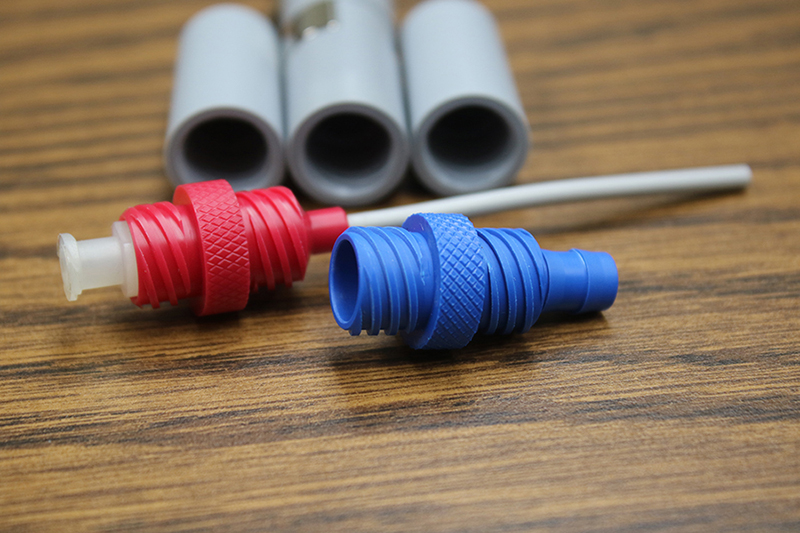
A medical parts distributor was in need of a field surgical device. The tool was to be made of plastic that would seal to keep the parts sterile. For that reason, the part could not be made with injection molded plastics. It required milled plastic. Boyer specializes in both metal and plastic milling. In this […]